Exploring the World of Plastic Molding Factories
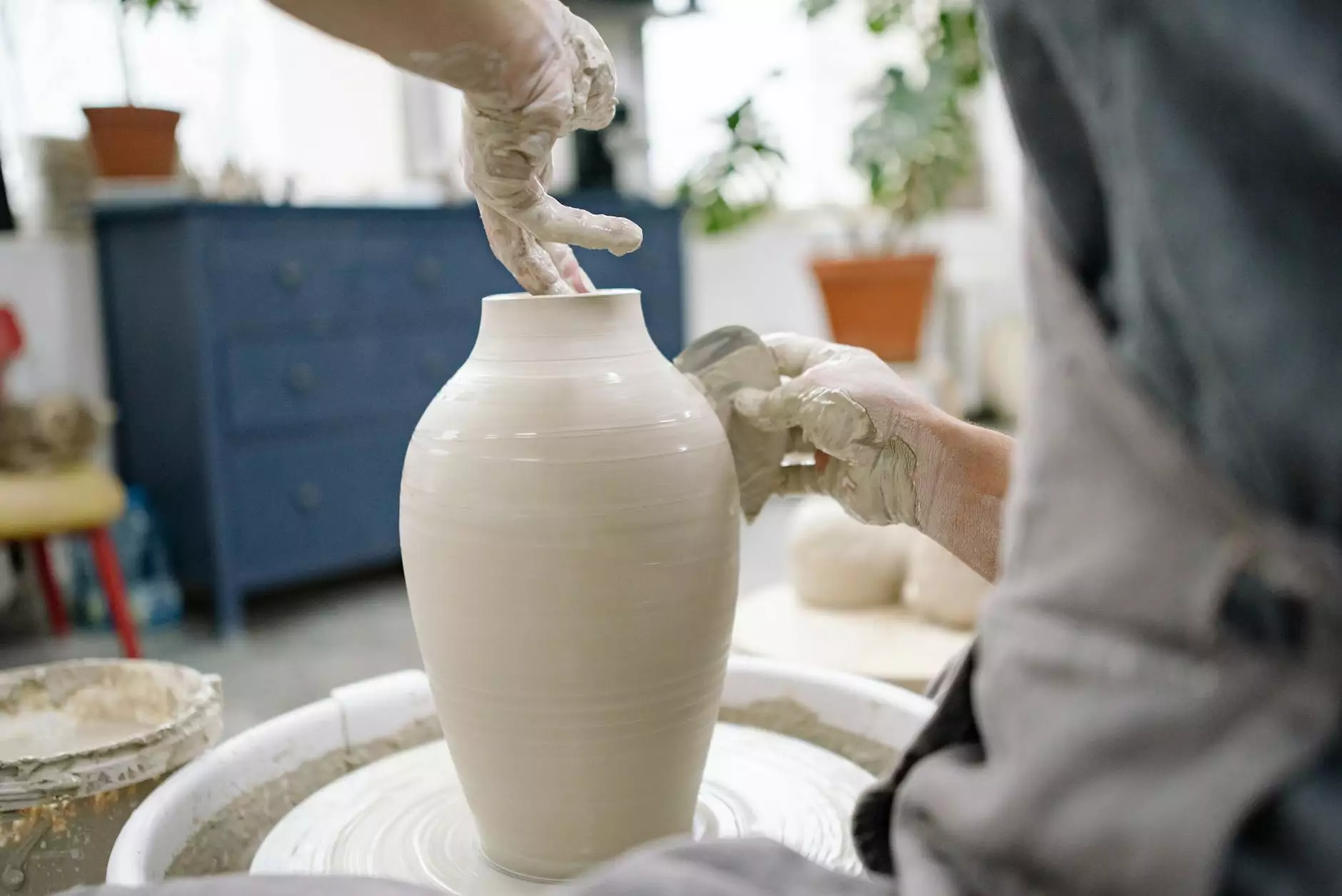
In today's manufacturing landscape, plastic molding factories play a crucial role in producing a myriad of products ranging from household items to complex automotive components. The versatility and efficiency of plastic molding techniques have made them a staple in many industries.
What is a Plastic Molding Factory?
A plastic molding factory is a specialized facility that utilizes various molding techniques to produce plastic parts and products through the manipulation of plastic material. These factories employ a range of technologies, including:
- Injection Molding
- Blow Molding
- Rotational Molding
- Compression Molding
Each method serves different purposes and is chosen based on the product requirements, production volume, and material characteristics.
The Importance of Plastic Molding
Plastic molding is an essential process in manufacturing due to its significant advantages:
- Cost Efficiency: High production rates and low labor costs reduce the overall expenditure for manufacturers.
- Design Flexibility: Complex shapes can be achieved with high precision, allowing designers greater creative freedom.
- Material Utilization: Minimal waste is generated during the molding process, making it an environmentally friendly option.
- Speed: Achieving consistent results in a fraction of the time compared to traditional manufacturing methods.
Types of Plastic Molding Processes
Understanding the different types of molding processes is key for businesses considering working with a plastic molding factory. Here are some of the main processes:
1. Injection Molding
Injection molding is the most widely used method in plastic manufacturing. This process involves injecting molten plastic into a mold to create parts. It is ideal for high-volume production and enables the production of detailed components.
2. Blow Molding
Blow molding is used to create hollow plastic parts, such as bottles. The process involves inflating a heated plastic tube until it touches the mold walls, forming the desired shape.
3. Rotational Molding
This method is typically used for creating large, hollow objects. Plastic resin powder is placed into a mold, which is heated and rotated to ensure an even coat of material.
4. Compression Molding
Compression molding involves placing plastic materials into a heated mold where they are pressed into shape. This method is often used for thermosetting plastics and can produce larger parts.
Key Benefits of Partnering with a Plastic Molding Factory
Choosing the right plastic molding factory can transform business operations, offering numerous benefits:
- Quality Assurance: Reputable factories maintain strict quality control standards to ensure products meet specifications.
- Scalability: Factories can scale production according to demand, making it easier for businesses to adjust their output.
- Technical Expertise: Access to professionals with specialized knowledge can optimize product design and manufacturing processes.
- Advanced Technology: Modern factories utilize the latest equipment, improving efficiency and product quality.
Applications of Plastic Molding
The applications of plastic molding are virtually limitless. Key industries that benefit include:
1. Automotive
The automotive sector relies heavily on plastic components for interior, exterior, and mechanical parts, taking advantage of the lightweight properties of plastics combined with durability.
2. Consumer Goods
From toys to kitchenware, consumer goods manufacturers utilize plastic molding to produce colorful, durable, and affordable products.
3. Medical Devices
Medical devices require high precision and sterilization. Plastics molded in cleanroom environments meet stringent regulatory standards.
4. Electronics
Plastic is widely used in the production of casings and components for electronic devices, enhancing design and functionality.
Environmental Considerations in Plastic Molding
As sustainability becomes increasingly important, plastic molding factories are adapting their processes. Strategies to mitigate environmental impact include:
- Using Recycled Materials: Incorporating recycled plastics into production.
- Energy Efficiency: Investing in energy-efficient machinery and practices.
- Waste Reduction: Implementing processes to minimize scrap and waste.
- Innovative Materials: Exploring biodegradable and compostable plastics.
Choosing the Right Plastic Molding Factory
When selecting a plastic molding factory, businesses should consider several factors:
- Experience: Look for a factory with a proven track record in your industry.
- Capabilities: Ensure they can handle the specific molding types and materials you need.
- Quality Standards: Verify they have certifications and quality control processes in place.
- Customer Service: Partner with a factory that values communication and customer satisfaction.
Conclusion
In conclusion, plastic molding factories are essential to modern manufacturing, driving innovation and efficiency across various industries. By understanding the multiple processes, benefits, and applications of plastic molding, businesses can make informed decisions that support their growth and sustainability goals. Transitioning to a robust plastic molding partner like Deep Mould can offer the competitive edge required in today's market.