Understanding CNC Machining Parts: A Comprehensive Guide
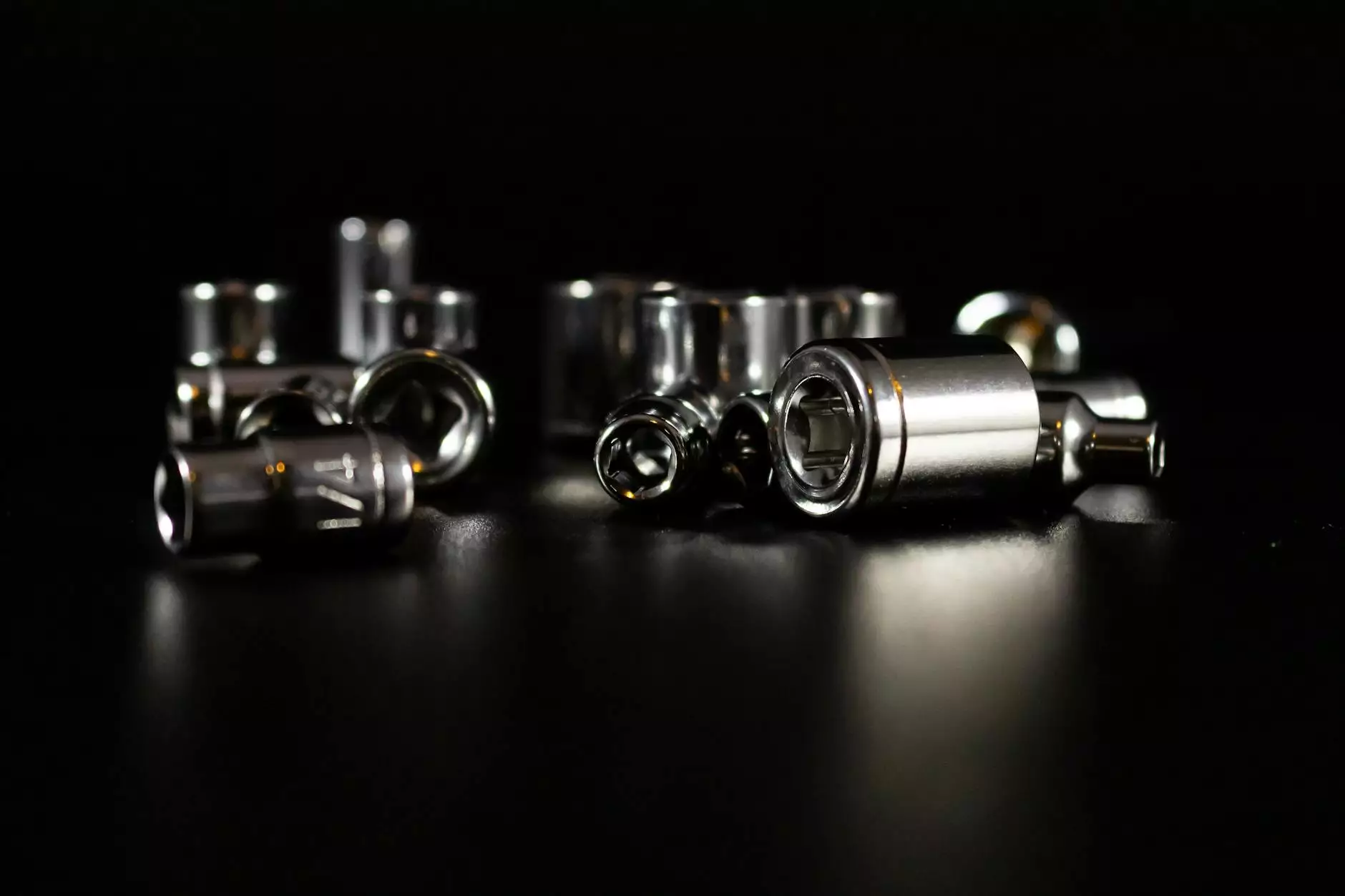
What are CNC Machining Parts?
CNC machining parts are precision-engineered components produced through computer numerical control (CNC) machining processes. This advanced manufacturing technique utilizes automated machinery, such as lathes and mills, which are guided by programmed instructions to create intricate and accurate parts from various materials, including metals, plastics, and composites.
The key advantage of CNC machining is its ability to produce parts with minimal human intervention, leading to consistent quality and high precision. Whether it's a prototype or a large production run, CNC machining allows manufacturers to meet stringent specifications and tight tolerances.
The Importance of CNC Machining in Metal Fabrication
In the realm of metal fabricators, the use of CNC machining parts is fundamental. Here are some reasons why:
- Precision: CNC machining offers remarkable accuracy, often exceeding tolerances of ±0.005 inches, which is crucial for industrial applications.
- Complexity: It enables the creation of complex geometries that would be impossible or prohibitively expensive to achieve through traditional manufacturing methods.
- Efficiency: CNC machines can operate continuously, significantly decreasing production time and increasing output.
- Customization: Manufacturers can easily modify designs and specifications without extensive retooling, allowing for greater flexibility and innovation.
The CNC Machining Process Explained
The process of manufacturing CNC machining parts involves several steps:
1. Designing the CAD Model
The first step is creating a Computer-Aided Design (CAD) model of the part. Engineers use specialized software to design the component, ensuring it meets all specifications and requirements.
2. Converting to G-code
After the CAD model is finalized, it is converted into G-code, a programming language that CNC machines understand. This code provides instructions on how the machine should move, what tools to use, and the sequence of operations.
3. Setup and Machining
Once the G-code is ready, the CNC machine is set up with the appropriate tools and raw material. The machine then follows the G-code instructions to precisely cut, drill, or mill the part.
4. Quality Assurance
After machining, the parts undergo rigorous quality checks using advanced measuring equipment to ensure they meet required specifications and tolerances.
Materials Used in CNC Machining Parts
CNC machining parts can be manufactured from a variety of materials, each offering unique properties suited for specific applications:
- Aluminum: Lightweight and corrosion-resistant, aluminum is commonly used in aerospace and automotive industries.
- Stainless Steel: Known for its strength and resistance to rust, stainless steel is ideal for medical and food processing applications.
- Plastics: CNC machining is also employed for plastic parts, where materials like nylon and polycarbonate are used for lightweight components.
- Brass: Brass is often used for electrical components due to its excellent conductivity and machinability.
Applications of CNC Machining Parts
The versatility of CNC machining parts allows them to be used in numerous industries, including:
- Aerospace: Components like brackets, housings, and mounts are machined with extreme precision to ensure safety and performance.
- Automotive: From engine parts to custom interiors, CNC machining is critical in the production of reliable automotive components.
- Medical: Surgical instruments and prosthetic devices that require exacting standards are often made using CNC technology.
- Consumer Goods: Many everyday items, such as electronic casings and housing units, are produced using CNC machining to ensure quality and consistency.
Advantages of Using DeepMould for CNC Machining Parts
When choosing a provider for your cnc machining parts, DeepMould stands out for several reasons:
- Expertise: With years of experience in the industry, DeepMould possesses the technical know-how to deliver high-quality parts that meet stringent standards.
- State-of-the-art Technology: Equipped with the latest CNC machinery, DeepMould ensures superior accuracy and efficiency in every project.
- Customized Solutions: DeepMould works closely with clients to develop tailored machining solutions that meet specific requirements, enhancing overall production outcomes.
- Commitment to Quality: Robust quality assurance processes guarantee that all parts produced by DeepMould meet or exceed client expectations.
Future Trends in CNC Machining
The field of CNC machining is continuously evolving, influenced by technological advancements and changing industry needs. Some future trends include:
- Automation and AI Integration: The incorporation of artificial intelligence in CNC operations is anticipated to enhance efficiency and reduce human error.
- Increased Use of 3D Printing: Coupling CNC machining with 3D printing technologies could offer innovative manufacturing solutions that benefit complex design requirements.
- Sustainability Practices: There is a growing focus on eco-friendly practices in machining operations, including waste reduction and the use of sustainable materials.
- Advanced Materials: Research into high-performance materials is likely to expand, leading to the development of CNC machining parts that are lighter, stronger, and more resistant to extreme conditions.
Conclusion
In conclusion, cnc machining parts play a crucial role in modern manufacturing, particularly in the metal fabrication industry. Their precision, efficiency, and versatility make them indispensable for various applications across multiple sectors. Choosing a reliable provider, such as DeepMould, ensures that you receive high-quality, customized components that meet your specific needs. As technology continues to advance, the future of CNC machining promises even more exciting developments that will further enhance its capabilities and applications.