Connecting Rods Manufacturers: The Backbone of Diesel Engine Performance
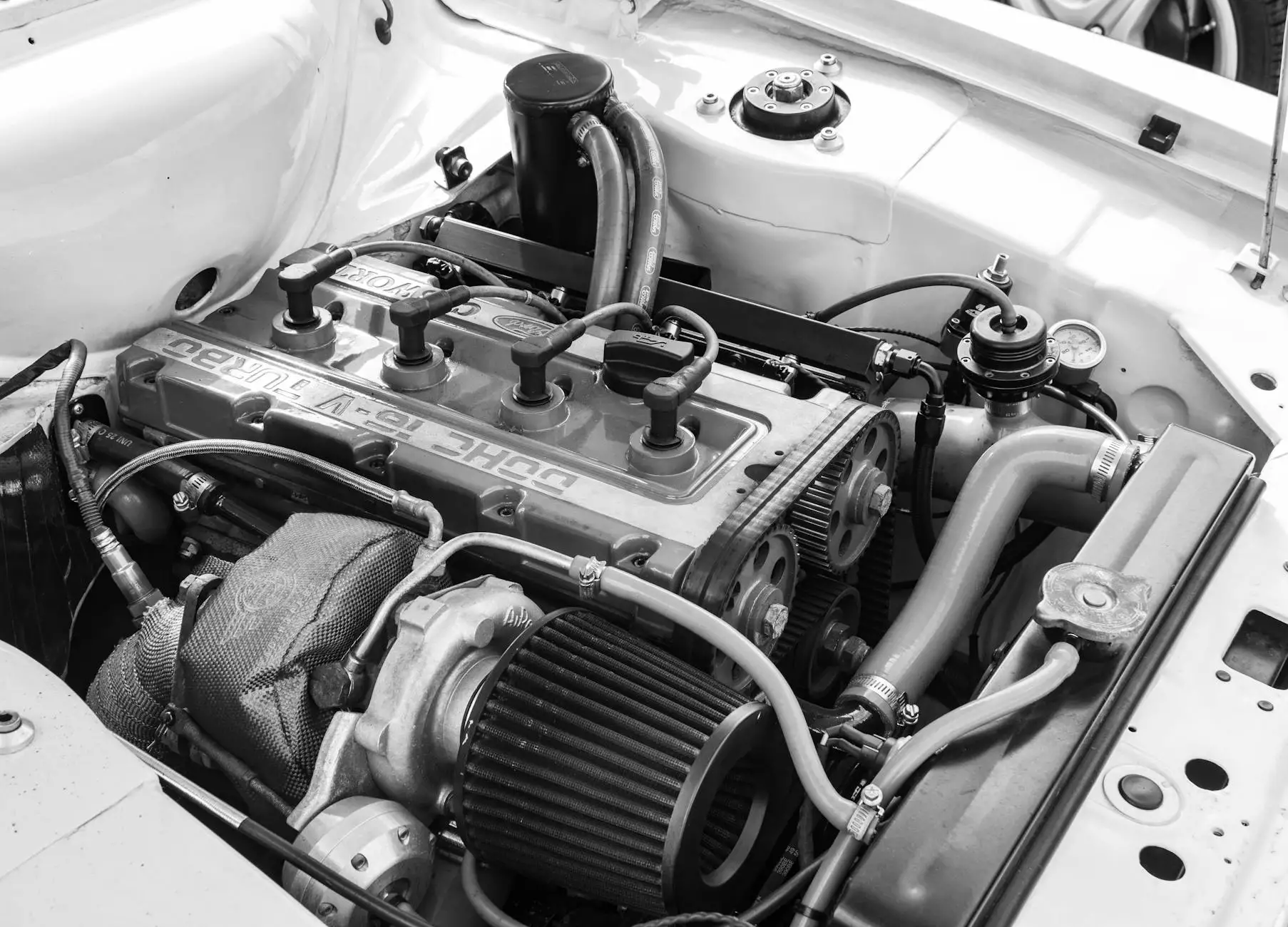
The world of high-performance diesel engines is one that relies heavily on the accuracy and reliability of connecting rods. These essential components play a crucial role in transferring power within the engine, significantly impacting its efficiency and overall performance. As the demand for high-quality diesel engines grows, so does the importance of connecting rods manufacturers in ensuring the longevity and durability of engine parts. In this comprehensive article, we will delve into the intricate details that make connecting rods a pivotal entity in the automotive industry.
Understanding the Role of Connecting Rods in Diesel Engines
Connecting rods serve the critical function of linking the piston to the crankshaft in an internal combustion engine. As the piston moves up and down, the connecting rod converts this linear motion into rotational motion, allowing the engine to produce power. The performance and reliability of connecting rods are vital for:
- Efficient Power Transmission: The design and material of connecting rods directly influence how effectively power is transferred from the piston to the crankshaft.
- Engine Balance: Properly manufactured connecting rods help maintain engine balance, reducing vibrations and wear.
- Durability: High-quality materials and precise engineering ensure that connecting rods withstand the immense pressure and heat generated within diesel engines.
Types of Connecting Rods Used in Diesel Engines
In the diverse landscape of diesel engines, various types of connecting rods are utilized. Understanding these types is essential for anyone involved in the production or supply of diesel engine parts:
1. I-Beam Connecting Rods
The I-beam shape is one of the most common designs for connecting rods. This design provides excellent strength-to-weight ratios, making it ideal for high-performance diesel engines. The I-beam connecting rod is capable of handling the extreme forces exerted during combustion.
2. H-Beam Connecting Rods
H-beam connecting rods are designed for additional strength, particularly helpful in high-performance applications where the engine is subjected to extreme stress. These rods provide increased durability and resistance to bending and deformation.
3. Forged Connecting Rods
Forged connecting rods are made from a single piece of metal that is shaped through pressing, producing a product with excellent tensile strength and fatigue resistance. They are often preferred in racing and heavy-duty applications due to their enhanced durability.
4. Cast Connecting Rods
Cast connecting rods are manufactured through a casting process and are generally more economical. They are suitable for standard applications but may not always handle the extreme conditions found in performance diesel engines.
Materials Used in the Manufacture of Connecting Rods
The choice of material used in the manufacture of connecting rods greatly influences their performance. Common materials include:
- Steel: High-carbon steel is widely used for its toughness and ability to withstand high-stress environments.
- Aluminum: Lightweight and used primarily in applications where reducing weight is crucial, but they may require more frequent replacement.
- Titanium: Known for its strength-to-weight ratio, titanium connecting rods are used in high-performance applications where cost is less of a concern.
The Manufacturing Process of Connecting Rods
The manufacturing of connecting rods is a sophisticated process that combines precision engineering with advanced technology. Here is an overview of the connecting rods manufacturers’ process:
1. Material Selection
The first step involves selecting the appropriate material based on the desired performance characteristics.
2. Machining
Once the material is selected, it undergoes machining to achieve precise dimensions that meet stringent specifications. This includes processes such as turning, drilling, milling, and grinding.
3. Heat Treatment
Many connecting rods undergo heat treatment to enhance their mechanical properties, making them tougher and more resistant to fatigue.
4. Surface Finishing
A smooth surface finish is essential for reducing friction and wear. Various processes such as shot peening or polishing may be utilized in this stage.
5. Quality Control
Quality assurance is paramount in the manufacturing process. Rigorous testing and inspection ensure that each connecting rod meets required standards before being sold to suppliers like client-diesel.com.
Market Trends in Connecting Rod Manufacturing
The market for connecting rods is influenced by several trends:
- Increased Demand for High-Performance Engines: As the automotive industry pushes for greater efficiency and power in diesel engines, the need for advanced connecting rod technologies is rising.
- Shift Towards Lightweight Materials: Manufacturers are increasingly looking to reduce vehicle weight without sacrificing strength, leading to innovations in material science.
- Sustainability Considerations: More manufacturers are adopting sustainable practices, focusing on environmentally friendly materials and processes.
Choosing the Right Connecting Rod Manufacturer
When selecting a connecting rods manufacturer, it is crucial to consider several factors to ensure that you are partnering with a reputable and capable supplier:
1. Reputation and Experience
Research the manufacturer’s history and client feedback. A well-established company with a solid reputation is often a safer choice.
2. Quality Assurance Processes
Ensure that the manufacturer has rigorous quality control procedures in place to guarantee high standards in their products.
3. Customization Options
Not every engine requires the same type of connecting rod. A manufacturer that offers customization can better meet specific performance and design needs.
4. Technological Capabilities
Modern manufacturing techniques and advanced technology in producing connecting rods can significantly influence the quality and performance of the final product.
5. Customer Support and Service
Look for manufacturers that provide excellent customer support to assist with any inquiries or issues regarding their products.
Final Thoughts on Connecting Rods Manufacturers
The role of connecting rods manufacturers is vital in the landscape of diesel engine parts and spare parts supply. By focusing on quality, advanced manufacturing processes, and innovative materials, these manufacturers contribute to the robustness of diesel engines across various applications. As the world moves towards greater efficiency and sustainability in automotive technology, the demand for high-performance connecting rods will continue to grow, making it a lucrative sector for both manufacturers and suppliers alike.
At client-diesel.com, we are dedicated to providing top-tier diesel engine parts and connecting rods that fulfill the demanding specifications of today's engines. Whether you are a manufacturer or a supplier, aligning with trusted and proficient connecting rods manufacturers is essential for operational excellence and client satisfaction in the evolving automotive market.