Precision Injection Molds: The Heart of Modern Manufacturing
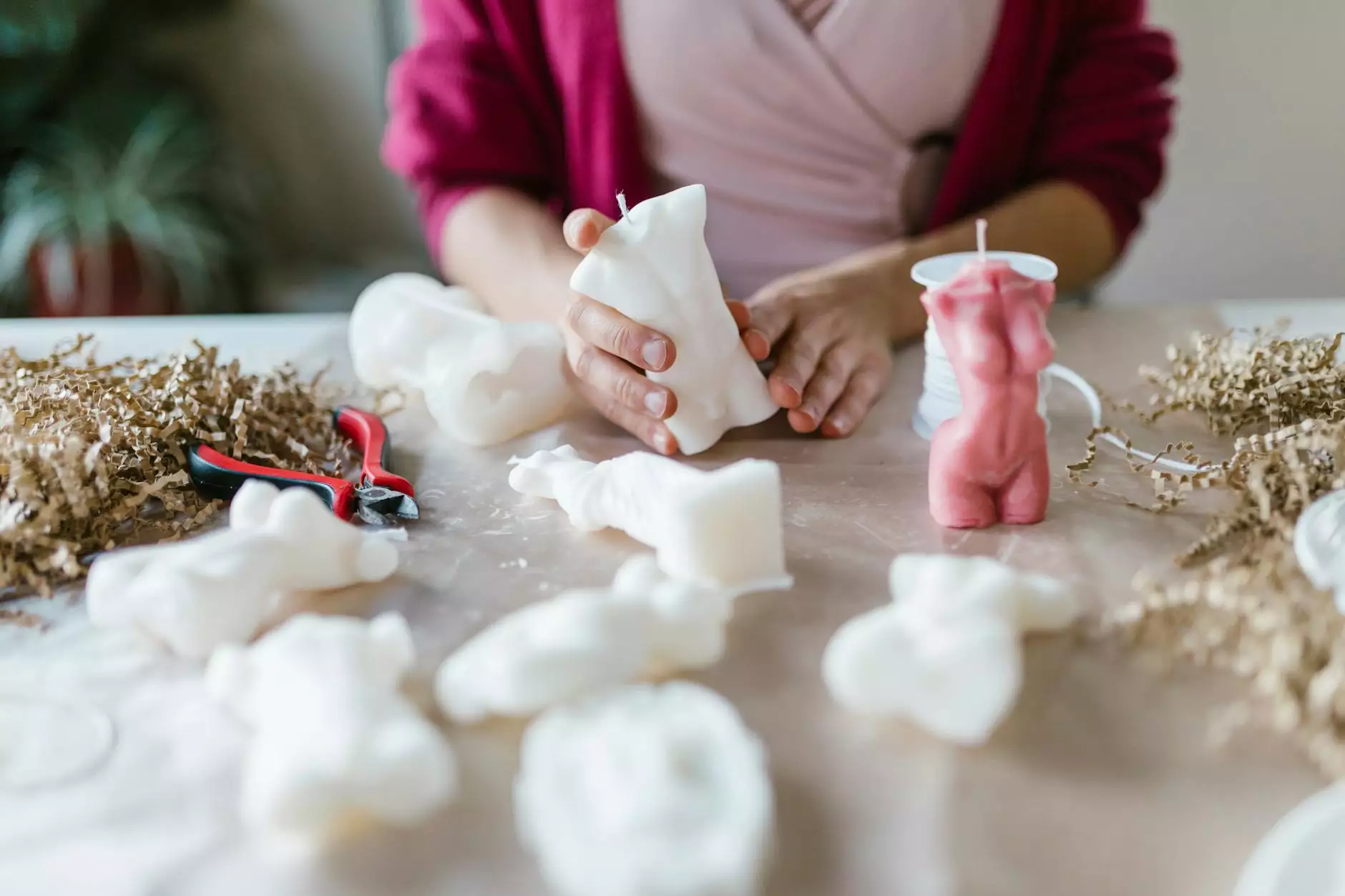
Precision injection molds are an invaluable asset in the manufacturing world. They provide unmatched accuracy and efficiency in producing components that meet rigorous quality standards. This article will delve into the intricate details of precision injection molds, exploring their design, benefits, applications, and the future of this foundational technology.
What Are Precision Injection Molds?
Precision injection molds are highly engineered tools used to create products through the injection molding process. This process involves injecting molten material, typically plastic, into a prepared mold to create a specific shape. The precision of these molds ensures that each component is produced with remarkable consistency and accuracy.
Key Characteristics of Precision Injection Molds
- Durability: Made from high-quality materials, precision molds are built to withstand the rigors of repeated use.
- Accuracy: These molds can produce parts with tolerances as low as ±0.001 inches, critical for applications requiring tight specifications.
- Customization: Molds can be tailored to specific product requirements, allowing for a diverse range of applications.
- Efficiency: Designed for quick cycle times, these molds help reduce production times and costs.
How Precision Injection Molds Work
The process of injecting materials into molds might seem straightforward, but it involves several complex steps:
- Mold Design: Initially, engineers design a customized mold based on the product specifications using advanced CAD software.
- Material Selection: The right plastic material is chosen based on the intended use, ensuring optimal performance and cost-effectiveness.
- Injection Process: The selected material is melted and injected into the mold under high pressure.
- Cooling: The mold is cooled, allowing the plastic to solidify and take the shape of the mold.
- Demolding: Once set, the mold opens, and the finished product is ejected.
Benefits of Employing Precision Injection Molds
The benefits of using precision injection molds are extensive, making them a preferred choice for many manufacturers:
1. Enhanced Product Quality
With the ability to produce parts consistently within tight tolerances, precision injection molds ensure that product quality is maintained throughout the production process. This minimizes defects and reduces waste.
2. Cost Efficiency
Although the initial setup cost for precision molds can be high, the long-term savings are significant. Efficient production leads to lower costs per unit, making high-volume manufacturing more economical.
3. Versatility
Precision injection molds can be used to produce a diverse range of products, from consumer goods to complex automotive components. This versatility allows businesses to meet various market demands efficiently.
4. Reduced Time to Market
The efficiency of the injection molding process, coupled with the rapid production capabilities of precision molds, significantly reduces the time to market for new products.
Applications of Precision Injection Molds
Precision injection molds are utilized across various industries, showcasing their versatility and effectiveness. Some of the prominent applications include:
1. Automotive Industry
The automotive sector relies heavily on precision injection molds for producing everything from dashboards to engine components. These molds ensure that parts meet safety and regulatory standards while being produced economically.
2. Consumer Products
From toys to kitchen appliances, consumer products benefit from the uniformity and precision that injection molds provide, ensuring that high-quality goods are produced at scale.
3. Medical Devices
In the medical field, precision is paramount. Injection molds are used to fabricate critical components for medical devices, ensuring they function reliably in life-saving applications.
4. Electronics
Precision injection molds facilitate the production of intricate electronic housings and components, enabling the creation of high-tech gadgets and devices that require meticulous detail.
DeepMould: Your Partner in Precision Injection Molds
At DeepMould, we specialize in developing high-quality precision injection molds tailored to the specific needs of our clients across various industries. Our commitment to excellence and innovation makes us a leader in the metal fabrication sector. Our team of skilled engineers and technicians leverage the latest technologies to design and manufacture molds that not only meet but exceed industry standards.
Why Choose DeepMould?
- Expertise: With years of experience in the industry, our experts understand the nuances of precision injection mold fabrication.
- Advanced Technology: We utilize cutting-edge machinery and software to ensure precision and efficiency in every project.
- Customer-Centric Approach: Our collaborative approach allows us to work closely with clients to deliver customized solutions that cater to their unique needs.
- Quality Assurance: We adhere to stringent quality control measures to ensure every mold we produce meets the highest standards.
The Future of Precision Injection Molds
As technology advances, the future of precision injection molds looks promising. Here are a few trends shaping the industry:
1. Increased Automation
With the rise of Industry 4.0, automation is becoming more prevalent in the manufacturing sector. This trend will enhance the production of precision injection molds, leading to even greater efficiency and consistency.
2. Sustainable Practices
As environmental concerns grow, the industry is shifting towards sustainable materials and processes. Future precision molds will likely incorporate recyclable materials and methods that reduce energy consumption.
3. 3D Printing Integration
The integration of 3D printing technology in mold production is opening new avenues for rapid prototyping and production. This will allow for greater flexibility and customization in precision molds.
4. Enhanced Simulation Technologies
Using advanced simulation technologies during the design phase can greatly improve the mold-making process, allowing for optimization before any physical production begins.
Conclusion
The role of precision injection molds in modern manufacturing cannot be overstated. Their ability to deliver high-quality, consistent parts across various industries is vital for sustaining growth and innovation. Choosing the right partner, like DeepMould, can help businesses leverage these molds to enhance productivity, efficiency, and ultimately, profitability.
As we look ahead, the continuous evolution of technology and methods in the field of precision injection molding promises to unlock new possibilities, further solidifying its place as a cornerstone of modern manufacturing.