Unlocking Precision and Efficiency with Die Casting Die: The Future of Metal Fabrication
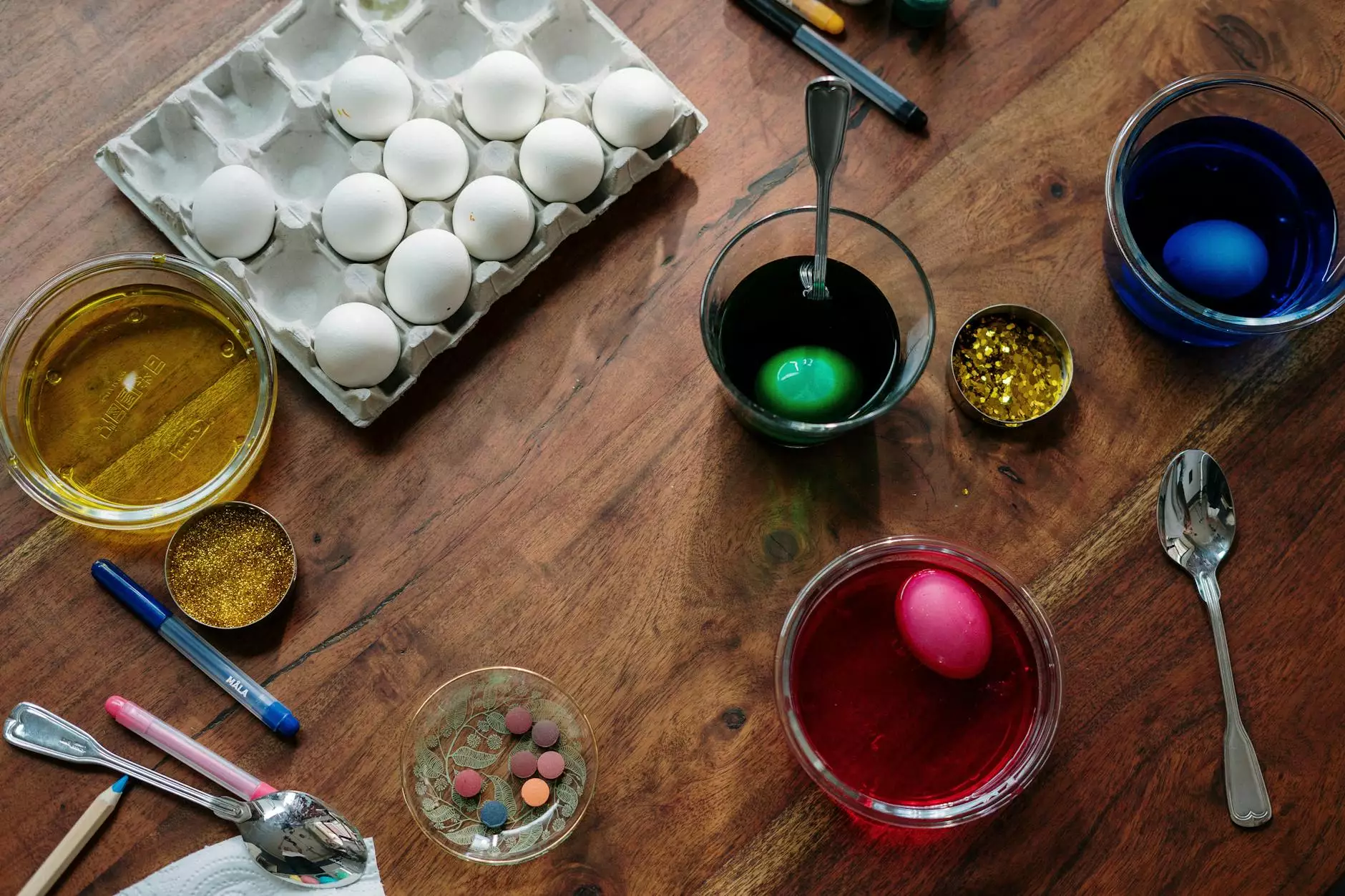
In the rapidly evolving world of metal fabrication, the demand for high-precision, cost-effective, and scalable production methods continues to grow. Among the various techniques available, the use of die casting die remains at the forefront, transforming industries with its unmatched ability to produce complex metal components efficiently and of exceptional quality.
Understanding the Significance of Die Casting Die in Modern Metal Fabrication
Die casting die are specialized molds crafted with extreme precision to facilitate the mass production of metal parts through the process of die casting. This method involves forcing molten metal under high pressure into a meticulously designed mold where it solidifies into the desired shape. The importance of die casting die extends beyond mere tooling—they are the backbone of high-volume manufacturing, ensuring consistency, durability, and superior surface finish.
What Makes Die Casting Die a Game-Changer?
The advantages of employing die casting die in metal fabrication are numerous and profoundly impactful:
- Superior Accuracy and Detail: Modern die casting die allow for the creation of highly intricate shapes with tight tolerances, essential for sectors like aerospace, automotive, and electronics.
- High Production Speed: The die casting process is remarkably fast, enabling the mass production of complex parts in a fraction of the time traditional methods require.
- Cost-Effective Manufacturing: Due to rapid cycle times and minimal post-processing, die casting significantly reduces overall manufacturing costs while maintaining high quality.
- Material Versatility: Suitable for a wide range of metals such as aluminum, zinc, magnesium, and copper alloys, making it adaptable across industries.
- Enhanced Structural Integrity: Components produced using die casting die exhibit excellent mechanical properties and durability, often exceeding those produced by other casting methods.
- Consistency and Repeatability: Once the die is designed and manufactured, it can produce thousands or even millions of identical parts with minimal variance.
The Die Casting Process: A Deep Dive into Die Casting Die Utilization
Understanding the process provides insight into the pivotal role of die casting die in achieving optimal results. The typical die casting cycle involves several critical steps:
1. Design and Engineering of Die Casting Die
Designing an effective die casting die begins with comprehensive engineering analysis. Mechanical engineers collaborate with clients to understand the specifications, function, and application of the final component. Using advanced CAD software, complex part geometries are modeled, considering factors like mold flow, ejection, cooling, and wear resistance.
2. Manufacturing of the Die
The manufacturing of die casting die involves precision machining techniques such as CNC milling, EDM (Electrical Discharge Machining), and surface finishing. High-quality die steels like H13 or Maraging steel are often used for their durability and heat resistance. Advanced manufacturing ensures that the die casting die can withstand millions of cycles, preserving dimensional accuracy over time.
3. The Die Casting Cycle
Once the die is manufactured, it is installed into the die casting machine. Molten metal is injected under high pressure into the die cavity, filling intricate shapes rapidly. After solidification, the die opens, and the finished part is ejected. This cycle is repeated continuously, producing high volumes of consistent components.
Customization and Evolution of Die Casting Die
Modern die casting die are not static. They evolve with technological advancements, allowing for tailored solutions that meet specific industry needs. Innovations include:
- Hot Chamber and Cold Chamber Die Casting: Different die casting methods optimized for various metals and production scales.
- Conformal Cooling Channels: Integrated cooling systems within the die to reduce cycle times and improve surface quality.
- Multi-Cavity Dies: Complex molds designed with multiple cavities for simultaneous production of identical parts, maximizing efficiency.
- Surface Treatments and Coatings: Enhancing die lifespan and surface finish quality through innovative coatings that resist wear and corrosion.
Industry Applications of Die Casting Die
The versatility of die casting die ensures its pivotal role across numerous sectors, including:
Automotive Industry
Automakers rely heavily on die casting for producing engine blocks, transmission cases, and structural components. The ability to create lightweight, durable, and complex parts directly contributes to vehicle efficiency and safety.
Aerospace and Defense
Precision-engineered die casting die enable the fabrication of high-strength, lightweight aerospace components, critical for aircraft and spacecraft applications where performance and safety are paramount.
Electronics and Consumer Goods
Electronics manufacturers utilize die casting to produce housing, connectors, and thermal management components with tight tolerances and excellent surface quality.
Industrial Machinery
Heavy-duty machinery parts, such as gearboxes and hydraulic components, benefit from die castings that combine strength and intricate design features.
The Future of Die Casting Die in Metal Fabrication
Looking ahead, the industry is embracing innovations such as smart dies integrated with sensors for real-time monitoring and predictive maintenance. Additionally, advances in materials, such as high-performance die steels and coatings, promise longer die life and superior component quality.
Automation and AI-driven design optimization tools are streamlining the development of die casting die, minimizing lead times, and reducing costs. With these technological advances, the metal fabricators industry will continue to push the boundaries of what's possible with die casting die.
Why Partner with a Leading Metal Fabricator for Your Die Casting Die Needs?
Choosing the right partner for die casting die manufacturing is crucial for achieving excellence at every stage. Leading metal fabricators like DeepMould bring unmatched expertise, advanced technology, and quality assurance processes that guarantee:
- Customized Solutions: Tailored dies designed to meet specific project requirements.
- Rapid Turnaround: Efficient manufacturing processes ensuring quick delivery.
- High Durability: Use of premium materials and coatings to maximize die lifespan.
- Technical Support: Expert consultation from design to production staging.
Conclusion: Embracing the Power of Die Casting Die for Future Growth
As industries continue to demand higher precision, complex geometries, and cost-efficiency, die casting die stands out as the ultimate tooling solution. The continuous evolution in materials, design, and manufacturing processes ensures that metal fabricators are well-positioned to meet the challenges of modern production.
Partnering with experienced professionals like DeepMould guarantees access to top-tier die casting die solutions that empower your business to innovate, scale, and succeed.
Unlock the Potential of Your Manufacturing Process Today
Investing in high-quality die casting die is not just about producing parts—it's about revolutionizing your manufacturing capabilities. From automotive to aerospace, every sector benefits from the precision, durability, and efficiency that only the best die casting die can deliver.
Begin your journey towards advanced metal fabrication solutions by collaborating with industry leaders committed to excellence and innovation. The future of manufacturing is here, powered by superior die casting die.